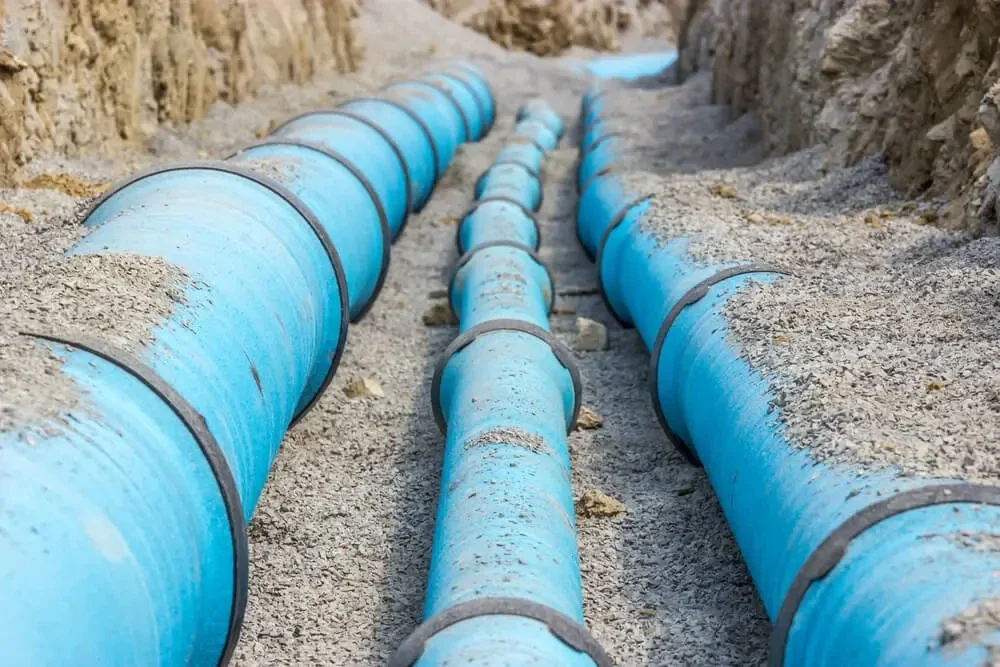
👋 Welcome! Here is a little bit about this personal project that I carried out as a duo team:
We were really interested in the water crisis that happened in Calgary in the summer of 2024. Therefore, we decided to create a project called InnoPipe Solutions. We wanted to find solutions to help make sure city emergencies like the one we just experinced doesn’t happen again. We have thoroughly documented two innovative ideas that we believe can help solve and prevent the water crisis from happening again. It would be great if we could have clean water forever!
We tried looking beyond the traditional methods of pipeline management. We created our projects using implementable technologies and methodologies, with the aim to revolutionize how we detect, maintain, and repair pipelines.
Each solution within the database is backed by research and engineering expertise, making them ready for immediate implementation.
We hope that **InnoPipe Solutions can empower industries to leap from outdated methods to the next level of advanced pipeline technology!!
Our story
We were so shocked when we first saw this news article in June, 2024:
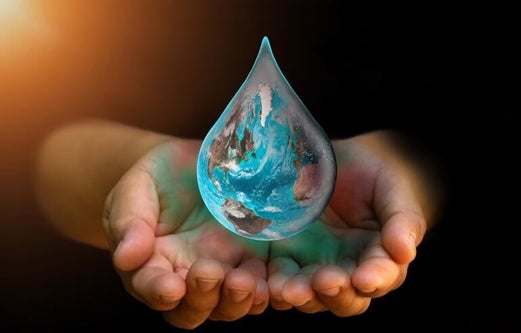
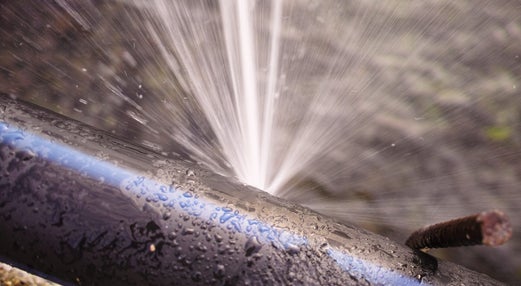
Curious about what sparked our interest? Take a look at this Medium article written by Xueqi.
Our Innovations and Solutions
InnoRepair Bot
There are many features to the InnoRepair Bot. Down below, we briefly summarize each:
Take a look at our pitch deck:

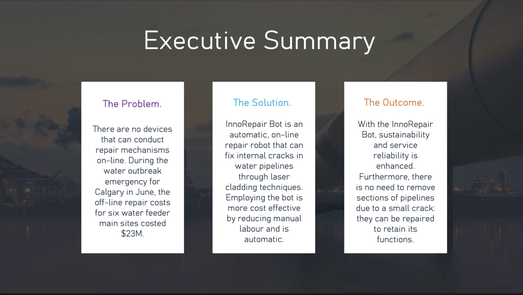
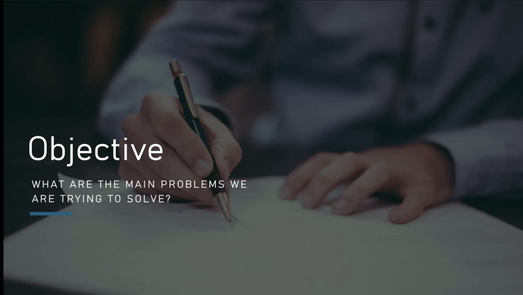

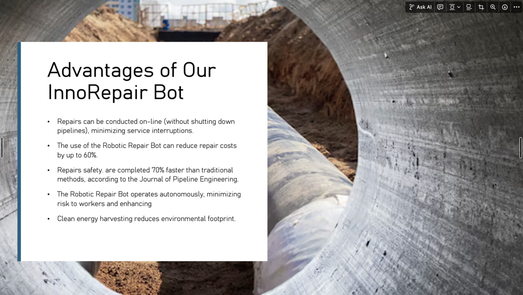
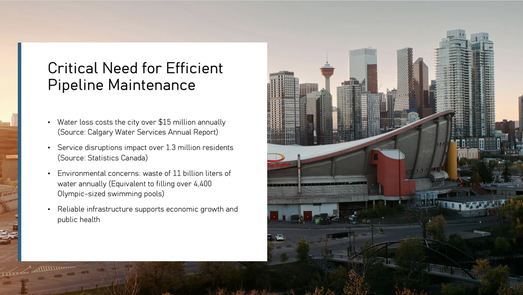
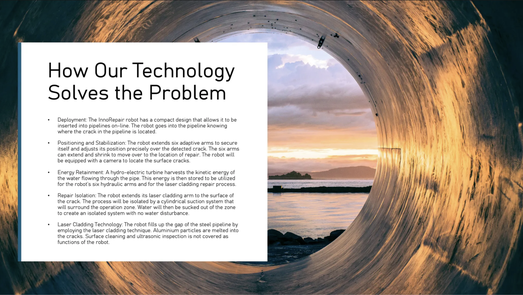
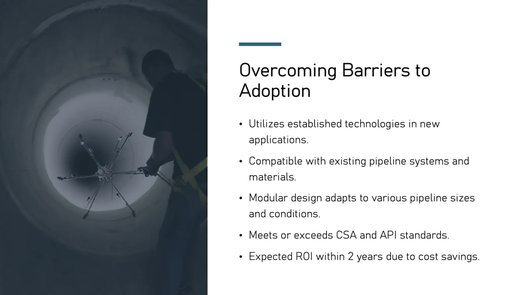
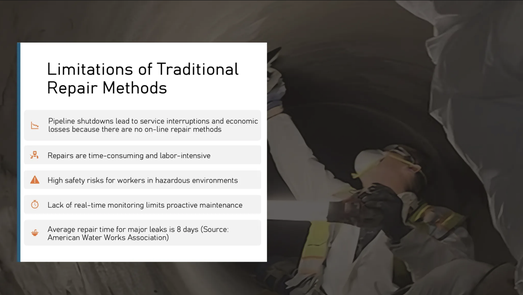
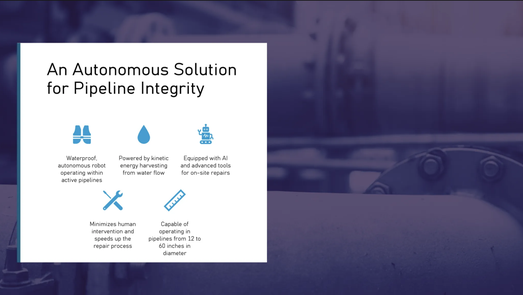
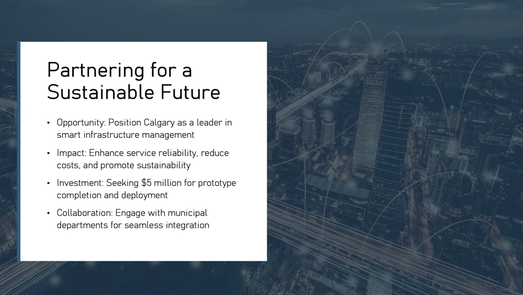
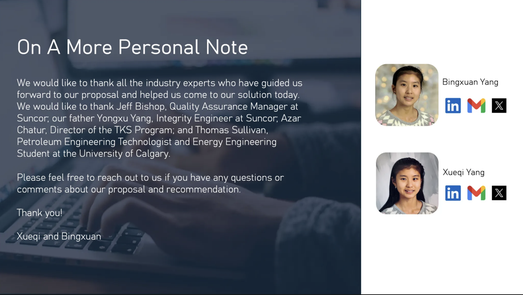
Youtube Video of the 3D InnoRepair Bot designed on CAD:
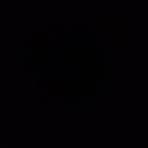
Concretene PCCP Pipelines
Here is pour
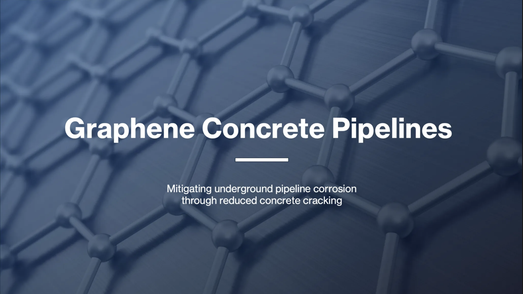
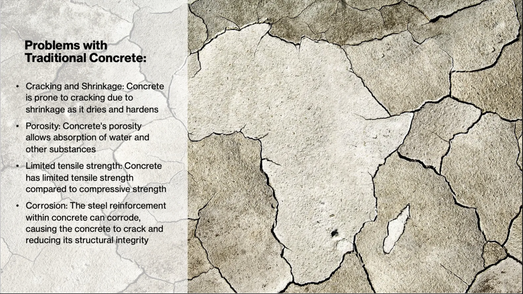
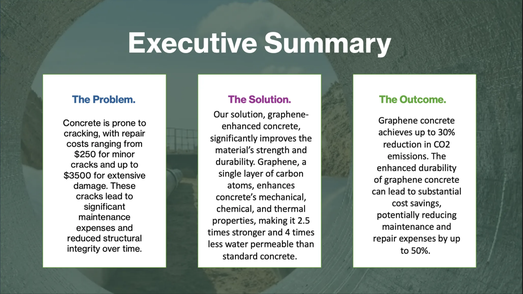
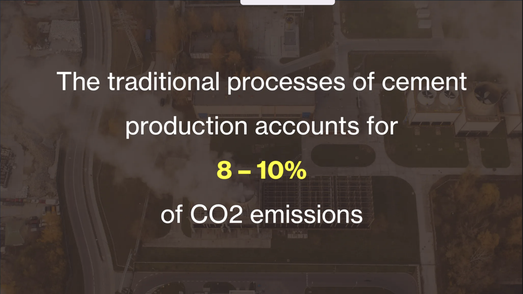
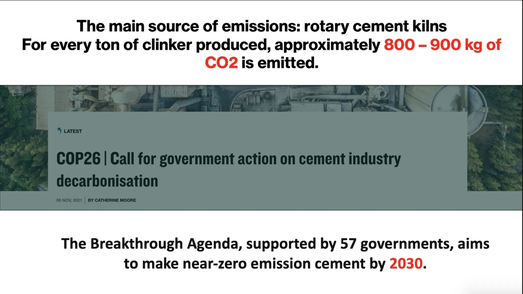
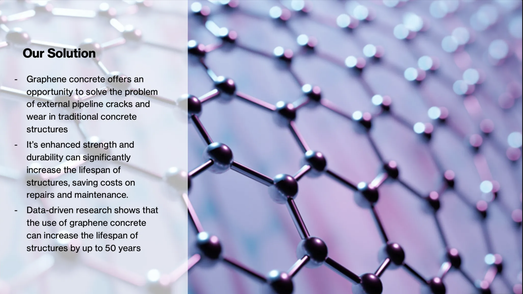
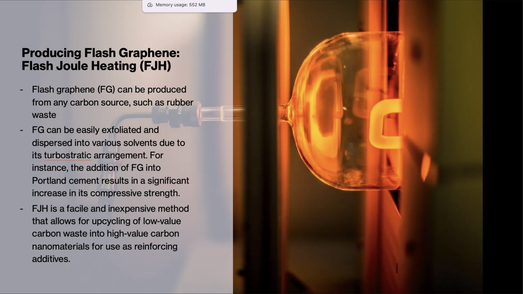
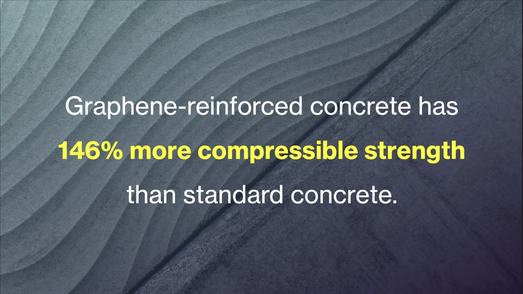
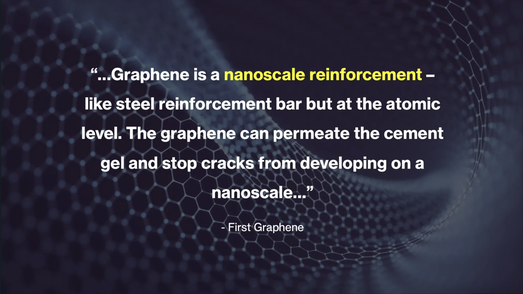
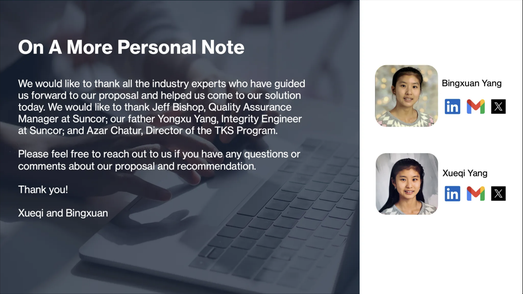
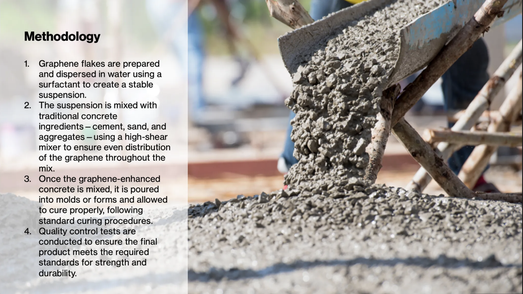
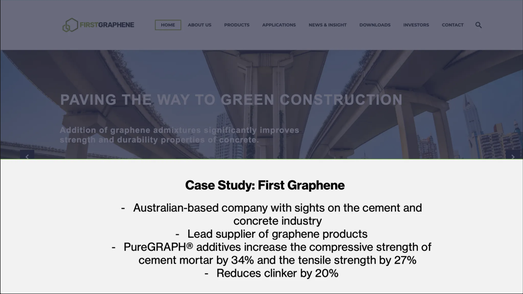
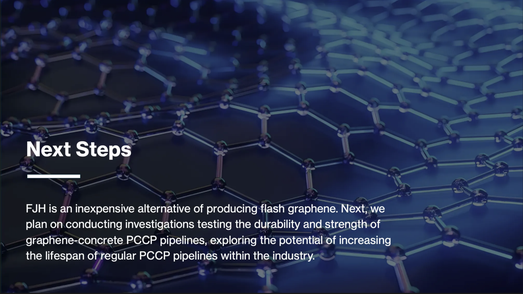
Add comment
Comments